[Note: this week was supposed to be the beginning of another glorious chapter in The Attack Of The Lesbian Squirrels. Instead I got crosswise with some pine in my workshop. It blew my scheduling all to hell. Y’all suppose that happens to real writers?]
[Edna Kampsett, the star of Road To Portland: Part 19: When Grammar Hurts, would like to point out that the initial version of this post listed options as 0, 1, and 3. Obviously that sort of Tomfoolery cannot be tolerated! Mr. Curmudgeon has had a stern talking to and a thorough beating. He has changed the options to 1, 2, and 3 and promises to never again post such shoddy work.]
I need help. Please advise:
Perhaps someone smarter than me (which shouldn’t be a stretch) can read my story and answer the age old question “should I drop cash on yet another damn powertool”. I keep thinking there’s a way to “old school” my way out of this but maybe not. This weekend my “old school” optimism kicked my ass bigly.
Here’s the background: I’m working on a “Project About Which I’d Rather Not Elaborate At This Time” (PAWIRNEATT should be a common acronym.) The goal here is to make a laminated “blank” that has the following characteristics; it must be strong, straight, reasonably light, and not warp. (The no-warp thing is where I stumbled into the whole lamination based vortex of doom.) Once I’ve made the object I’ll “shape” it further. (Which is why I didn’t just go with a chunk of plywood or something. A decision I may have made incorrectly?) The end product will not be merely rectangular in cross section.
Also, and this is a new component to my workmanship, I’d like it to not look like a chimpanzee made it. (Who knows if I’ll clear that bar.)
I picked through the local wood supply like I was sifting for gold and got the best material I could find, which wasn’t very good. Then I spent eleventy zillion man hours milling innocent 2″ thick dimensional pine stock through my table saw. I hoped to come up with a series of staves about 1″ x 1 1/2″ that were knot free and arrow straight. Fat chance. The wood was shit and mostly I made sawdust.
Being the kind of guy who cannot quit, I picked the best of the mountain of source material I’d created and soldiered on. I slathered the staves with two part epoxy mixed with wood flour and clamped them as straight as I could.
And… it sucked. Some of the wood warped a bit up, some warped a bit down, and lots of it was goobered with epoxy. It reminded me of Satan’s badly made PB&J sandwich.
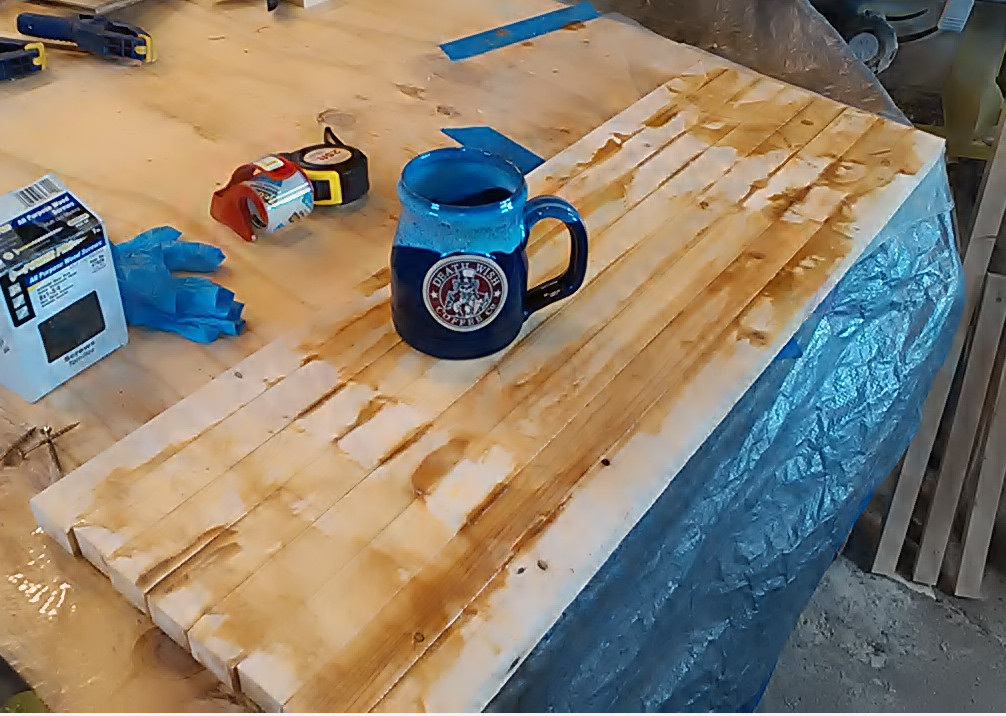
I’ll admit that I got a little out of hand with the epoxy/filler material. Also note the subtle product placement for my favorite coffee brand. (Considering how much I drink, they ought to sponsor me.)
I thought this was OK. In fact I smugly thought I had it well in hand. Knowing my incompetence, I’d planned for the laminated “blank” to be a bit oversized, thinking I could shave it down to perfect and remove the crappy surfaces.
I needed about 11″ wide x 3′ long by 7/8″ thick. So I’d made it about 12″ x 3’+ a smidge x 1″. Aint I clever?
I just barely managed to trim the ends with my radial arm saw. Another 1/2″ and it would have been an issue. But it worked so there’s that.
To rip it to width I scribed out lines (carefully cutting more off the ugliest edge) and…
MICE BUILT A GOD DAMNED NEST IN MY BANDSAW! THOSE BASTARDS!!!
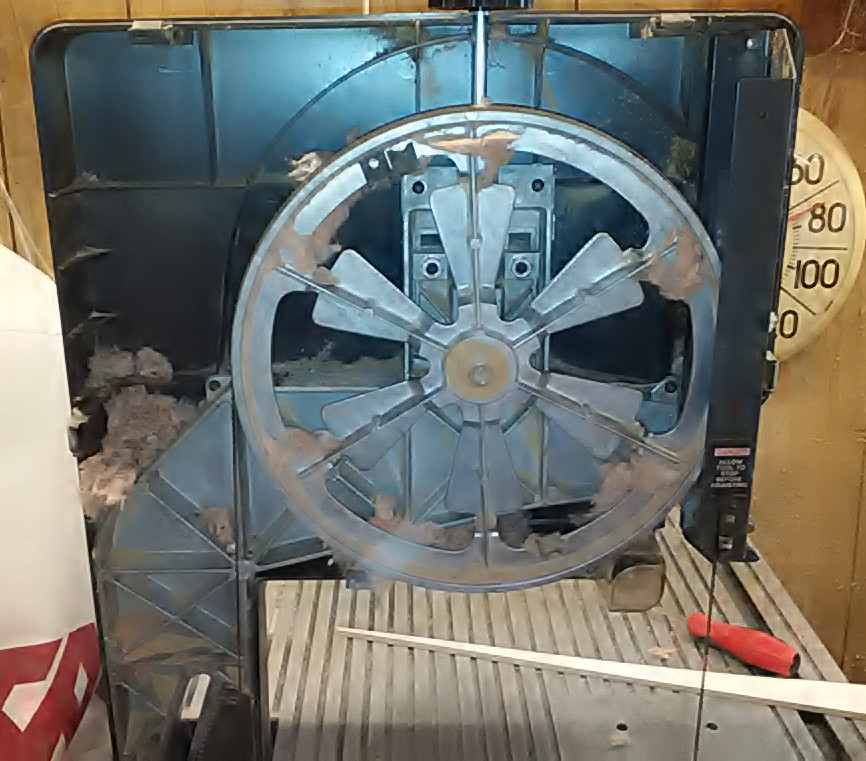
This is AFTER a half an hour attacking the mess with a shopvac.
OK, so now I’ve been at it forever and I’m tearing apart my bandsaw and I’m pissed. Shit happens and there was nothing I could do but vacuum accumulated evil from my equipment. I could have used the table saw but there weren’t any edges I thought were 100% perfectly straight. Plus I felt like like using my bandsaw.
So far so good.
Now I was looking forward to the zen like use of my trusty low angle block plane. Oh man this was going to be awesome! Well I got zen like labor alright. I got it good and hard. Hours of it. I tried my random orbital sander and that wasn’t much help (maybe a huge belt sander would’ve been a different story?) So it was back to the plane and I was not easily dissuaded. I kept at it forever. My arms are toast, my shop is filled with poetic little shavings, and I’m still 1/16″ too thick. Good gravy, a man only needs so much “wax on, wax off” zen-like work before he’s fuckin’ had enough.
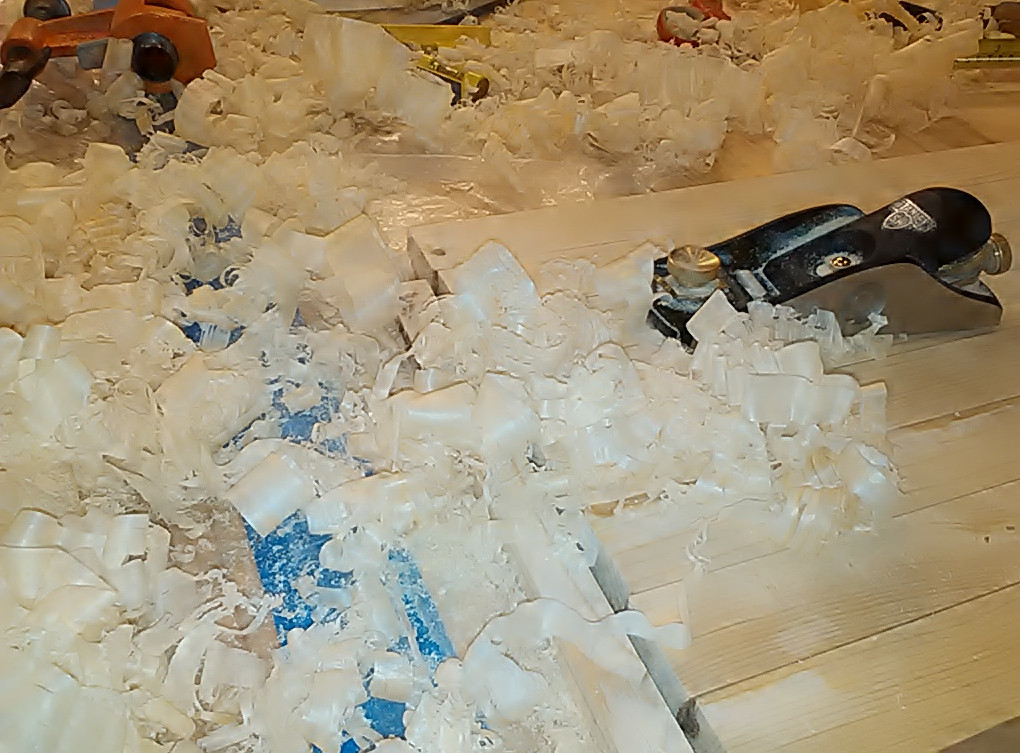
This is but a tiny fraction of the giant mountain of shavings that I created by slowly and steadily beating myself to death over several hours.
So that’s where I am right now. The laminate blank is properly dimensioned in the X and Y axis but Z kicked my ass.
Now here’s the part where I admit defeat. This was a single 3′ laminate blank, I’ve “invested” far too many man-hours, and even if I “nut up” and plane away until I’m done…it’s not truly done. I’ve got to make a second and even bigger blank (about 4′ long). If one beat me this bad, a second is going shave my liver and hang it from a flagpole.
For now, I’ve closed the door on my workshop and fled. What shall I do to equip for the next sortie in this battle?
Option 1, The Current “Gettin’ My Ass Kicked” State Of Affairs:
This is what I’ve been using. It’s sweet and beautiful but apparently inadequate for taking an 1/8″ layer of pine and epoxy off 3 square feet surface area (6 feet if you count both sides). I swear I mentioned this thing sometime this spring when I bought it but I can’t unearth the link. Anyway I like my plane and it’s excellent for realistic use but it’s just too small for 11″ wide.
Option 2, The “Fuck It I’ll Solve It With Horsepower” Method:
This is what I’m considering and is probably the no-brainier correct American solution? Lord help me, I don’t want any more expenses but I’m pissed off and caressing my credit card. It seems like the only solution. I doubt I’ll use it very often. Also I have no idea if the one in this link is a good deal or shit in a plastic housing. I’m not in the market for a “last forever and good enough for a precision craftsman” tool; “good enough” is my budget.
Option 3, The “Be Cool Like Roy Underhill” Hail Mary Pass:
This would be cool, if it worked and it was (much) cheaper than a powered thickness planer. I have my doubts. I’ve had far too much character building in this project and I don’t want to buy some museum piece that’ll wear me out. I’m willing to entertain the idea but I only want to buy one plane and it’s gotta’ work right out of the box.
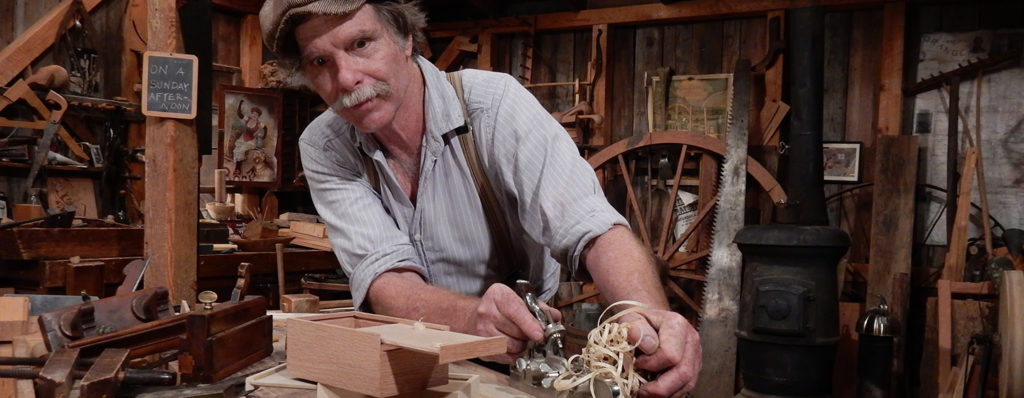
Roy Underhill is cooler than me. He never killed half a weekend trying to make a single damn blank.
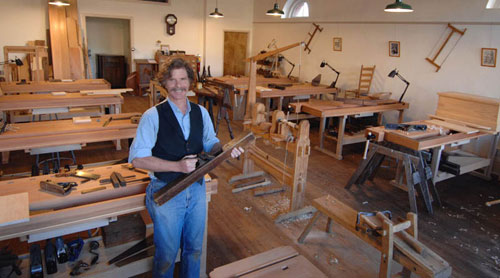
Here, Roy demonstrates his unlicensed, high capacity, +2 planer of smiting! Combined with his hippie powers and woodworking wizardry he’s a sawdust master.
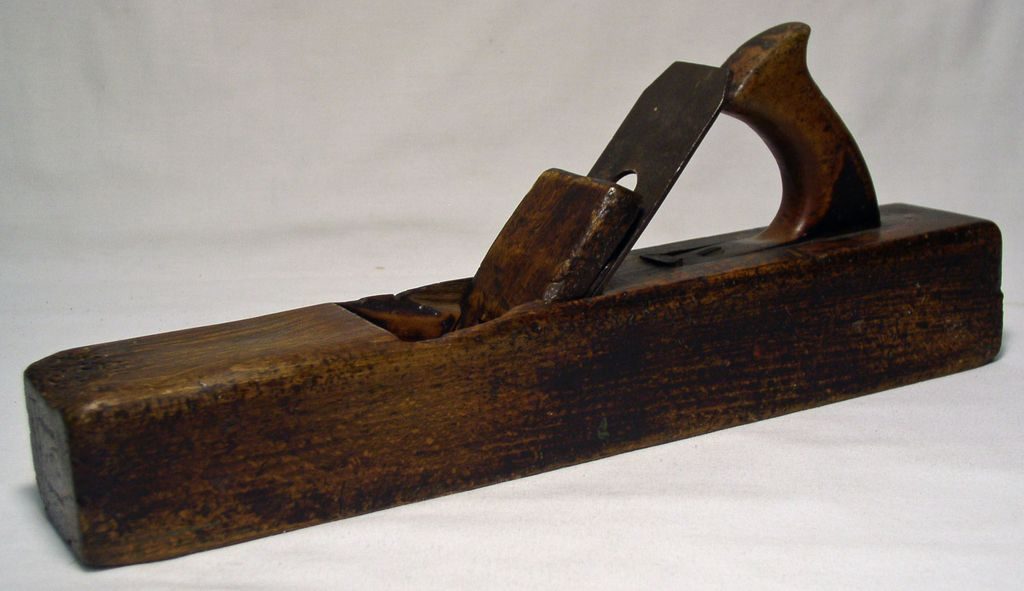
This is super cool but where is the “on button”? I can’t even pretend I can use it without instruction.
Also, what the hell is happening here?
So… what now? All advice is appreciated.
Several different ways you can go:
1. Keep going with the hand plane, it’ll eventually work, and you’ll burn some fat off doing it. (but look into getting something like a jack plane instead for faster stock removal, then finish with the smaller bench planes)
2. Get a hand belt sander. I use a Ryobi (yeah, I know, Ryobi…whatever. It works, and keeps working. Been using it for years, can’t see the benefit of Bosch, etc) 21″x3″ model. Get various grits, it’ll tear through stuff. Sometimes too fast..so can be iffy if you’re trying to sneak up on a certain dimension.
3. Thickness drum sander. Pricy, messy, and handy as hell sometimes. I still don’t have one. But you’ll find that most of the folks that do quite a bit of thickness work will have one.
4. Bench top thickness planer. I have a Dewalt model, again, using it for years, and it’s come in very handy many times. You can be done in a few minutes what might take you an hour to plane down by hand. Of course, you can also screw things up quite nicely in a few minutes.
I don’t know what kind of work you do, but if you do anything off site, or need to work on things that are already installed (stair treads, I’m looking right at you, damn you), then get a hand belt sander. Mine gets continuous use.
You’ll get faster, more precise results with the bench planer – but it’s gonna cost you. Then again, if you’re doing this often enough, it’s worth it.
No idea on the Wen, never seen one in person, so can’t offer an opinion.
At the least you seem to be OK on sharpening your planer blade.
Belt sander, 60 grit and work down.
You really need a bench planer. You wouldn’t drill a bunch of holes with a hand drill, would you? Power tools make the man. Visit your local pawn shop, pick up a used bench planer, sell it back when you’re done.
Anybody close by with a thickness planer? I mean someone you can trust your PAWIRNEATT with? Maybe you can barter in bacon.
Bartering is a manly outcome, as opposed to conceding defeat to mere pine.
I’m right there with ya. Also scrounging and hunting. I managed to get a sawdust vac from craigslist via searchtempest far from my home. I think the vac was witness to a calamity, but that’s another story and it works great for me.
get two 7/8th inch square tube steel at junk yard
you know that hole every hand saw has in it for hanging on walls? attach bolt there.as handle
find second person.
Place both tube steels next to project, clamp with those giant clamps your kid probably pretended were swords once. (thats how I describe them, sword clamps. they probably have a real name)
Cut using handsaw as a two person saw. Use sand paper to pretty it up.
Thats all i can think of if you dont want to plane anymore or buy something expensive
That would work but I may be willing to blow money to avoid that much labor.
Understandable. I’m still at the age where getting paid in pizza and beer sounds like a good deal.
There’s never really an age when getting paid in beer and pizza sounds like a bad thing. Once it’s implanted it never goes away. It’s a good personal philosophy!
But I’m at an age when I ought to be smart enough to know I’ve got other options. I can cut a check and “solve a problem” and yet I still feel like I’ll be living in a “van down by the river” if I “waste” three C-notes. This is half math and half me being a cheapskate. Also there’s the age when “is this tool cheaper than a series of chiropractor visits” comparison starts favoring the machine. Time waits for no man.
I fear that the combination of thickness planer and epoxy would result in disaster. I agree with Czechsix that a thickness sander is the optimal solution. If flatness of the surfaces is not critical, a handheld belt sander will work. I have a Craftsman 4×24 that is well over 20 years old.
So what you’re really looking for is something like this:
http://tinyurl.com/y899gq6l
but slightly thicker?
And there’s also these guys:
http://www.theworkbench.com/edgegluedpanels.php
But then the squirrels might need a planer or a belt sander…
Jesus! To think I coulda’ spent $7.38 at Lowes for the finished part? Egad! The mind boggles at all that “wasted” work! For my own sanity I’m going to pretend that was an impossible approach.
Well to be honest, I would expect that the glue bonds from a company that makes such things commercially will probably be slightly better than what you will achieve as well…
Now you’re just putting salt in my wounds.
Just tryin’ to give you the facts, Jack!
If’n you need a planer for other things, then by all means get one. But if this is a one-off project, why buy the cow when you can get the milk for almost free???
Easy answer. Why do you drink Death Wish instead of Maxwell House?
You are a man. Men NEED machines.
By George you’re right! SInce when do I apply logic on the homestead!?!
A man who writes about squirrels and put a high speed chassis on his woodsplitter shouldn’t fret over a few hundred on another tool. I like your way of thinking!
if you go with thickness planer… You will use it again and again.
Plane pieces before cutting to length and gluing.
There’s an occurrence called sniping where the planer gouges the wood a few inches before the end and the end comes off rollers.
I followed you right up to the point you asked if you needed a new power tool. You lost me at that point, as everything stopped making sense.
A planer is exactly what you need here, the rigid from home depot is the recommended last forever, accurate as you’ll ever need and only cost about $100 more option
A Rigid thickness planer is how much? Did I read that as $100? Wow that’s cheap. If that’s the price I’ll have one by sunset.
I interpret the comment as meaning $100 additional over the $241 option you originally had.
That makes a hell of a lot more sense. I was wondering what I was missing. I probably needed more coffee at the time.
I use the shit out of my thickness planer but then I do a lot of craftsy stuff that justifies the purchase. I’ve got hand planes out the wazoo, a couple of belt sanders and have used them to achieve what I needed. My shoulder had dictated over the last few years that I can either quit my hobby or buy tools that take the load off my rotator cuff. I like my TP. I even build a sled that lets me use it as a jointer. Then I bought a jointer using the same shoulder excuse. Then a small CNC. Then….
I need a 12 step program for tools.
I must admit my arms are killing me today. Perhaps “old school” is just a PITA in this case.
As for your stuff; I’ve always figured once a man crossed the CNC event horizon he had more or less become a newly evolved, self-made, species of concentrated awesome. I don’t have a CNC and wouldn’t know what to do with one if I did, but I’d love to have one cluttering my garage.
The CNC sat in that overcrowded part of my brain called “want bad” for a couple of years. Finally the stars aligned, I got a paying side job that could justify it and then boom, a random scratch off then a small bonus threw a chunk of change my way. The Gods had smiled down on me for enough to get the machine and a new 30-30. Been puttin’ holes in stuff with both ever since.
I’m with the majority here: get the thickness planer. Really, if you ever make things that aren’t the size of the finished lumber off the rack from the Orange or Blue Borg, you need one. I bet that Roy Underhill has one secretly stored off set and uses it when the cameras are off. The only reason I don’t have one is that I don’t do much woodworking anymore.
I’m kind of crossing the event horizon into Luthiery, and find that guitar makers tend to use thickness sanders. Maybe because they’re working on pieces maybe 1/8″ thick and reducing by 10 or 20 thousandths.
Chris Schwarz, author of ‘The Anarchist’s Tool Chest’ uses a thickness planer. I have a god knows how old Porter Cable model, which is pretty much the same as the current Dewalt and Rigid ones, and it’s still working. I can do it with hand planes, but a decent jack plane, with the extra blade you would need, will cost you as much.
No shit?
If the “Anarchist’s Tool Chest” guy uses a thickness planer I certainly shouldn’t feel lame for using one. His stuff is way cooler than the crap I build.
By the way, did you biscuit them together? Or doesn’t the strength of the glue joint really matter that much?
I did not biscuit them together but I think the epoxy joins are sufficiently strong. I took some scrap and did a similar join and it seemed good enough. Also the PAWIRNEATT has structural components that’ll compliment the joins. Thanks for askin’ though.
Thickness planers are lovely tools which would make short work of the piece described above. Recommending whether or not you should get one, or what quality level you should seek requires a bit more E about your P* in the aforementioned PAWIRNEATT.
That said, if you prioritize the avoidance of spending money above good sense, and want an excuse to screw around in the shop while thumbing your nose at the fine woodworking types, I submit the following bit of ad-hoc tomfoolery:
Per the above, you have a perfectly good table saw, yes? Get the faces relatively flat with the hand plane. Set the rip fence and blade height to take off the stock one blade width at a time, moving the rip fence to take the next pass. Once you get about halfway across the board, start supporting the cut side with a sheet of material the approximate thickness of the material you are removing (what for keeping your work piece relatively flat) .
This will remove the bulk of the stock in approximately a half- hour per side, if you average a pass every 15 seconds. However, If you have a dado set you can speed this up by 6-10x (if you do not have one, dado sets are much cheaper than even the crap planers). Leave a bit of stock for cleanup with hand plane/sander/scraper.
*Belay that. Under no circumstances am I interested in further elaboration regarding your P**
**Like potty humor? Urine luck; I am an ex-spurt!
Start looking at the auctions in your area. I am picking up shop cabinets, tools and supplies for cheap. In a 50 mile radius I have 5 auctions to peruse on tuesdays and wednesdays. Picked up an old cast iron framed miter saw for 15 bucks, included the saw. Now looking for a band saw and maybe a planer. If you want to have a look see – go to Excess Recover Solutions or Biddergy or Simple bid (these are in Benton Harbor, Kalamazoo and Grand Rapids respectively. There have to be similar in your area.
Unless you get a monster planer you will eventually get to a piece of lumber that doesn’t fit.
https://www.lie-nielsen.com/product/bench-planes/low-angle-jointer?node=4065 Woodcraft probably has a cheaper version. Even Stanley has been producing some interesting planes lately.
Expensive, but will last several lifetimes if taken care of. This isn’t where I would start though. Take out most of the material with a jack plane. (Or even a scrub plane. Info on YouTube on how to turn
a cheap HF plane into a scrub plane)
That said, a thickness planer makes it really easy to buy rough-saw lumber. Which means your table tops are not 3/4 inches. I hate 3/4 inches mostly. (Everything looks like it came from IKEA when it is 3/4 inches thick.)
OMG… that’s so beautiful!
Initially that’s the sort of solution I was seeking. Then I gave in to the dark side and went with a 15 amp motor (which cost about the same thing). This is one time when I took took the path more traveled.
If you don’t mind me asking, what’s a more excellent thickness? 7/8″? 1/2″? 1 1/4″?
I haven’t a clue and am suddenly thinking about planing stuff.